BOPP film is currently the most popular material for modern flexible packaging in the food, perfume, tobacco, pulp and paper, and consumer goods industries.
Previously, we faced situations when the width of the BOPP film roll after cutting did not meet the required values, the tagger could not visually see the error, and after shipment, a problem in our customers' production occured. In some cases, the entire shipment had to be returned and re-supplied. By applying a robot that controls BOPP film rolls geometry, such situations will be eliminated and losses will be minimized.

The robotic system handles 79 types of BOPP film and rolls from 30 cm to 2.5 m wide, and processes 1 roll per minute or 1,440 rolls per day. The system controls roll width with an accuracy of 3 millimeters, and measures roll weight and diameter. In case inspection proves successful, the products are marked accordingly, and in case of defects, the problem is reported to the operator.
KUKA KR 60 L30-3 industrial robot based on KR C4 controller integrated in the robotic process system is equipped with a barcode scanner, a special device for measuring the object geometric characteristics and a vacuum gripper for applying labels. Using a scanner, the RPS reads product data from a process barcode containing information about the order, BOPP roll geometry, and weight. Then the manipulator robot performs a series of measurements on the diameter of the roll entering the weighing section, measures its actual dimensions. RPS automatically checks whether the received data from the process barcode matches the actual measured roll data. If the product parameters fall within the technical specifications, the system registers the fact of finished product manufacture in 1C and sends a request to print two labels, and the manipulator robot applies these labels to the inner and outer diameter of the roll, respectively.
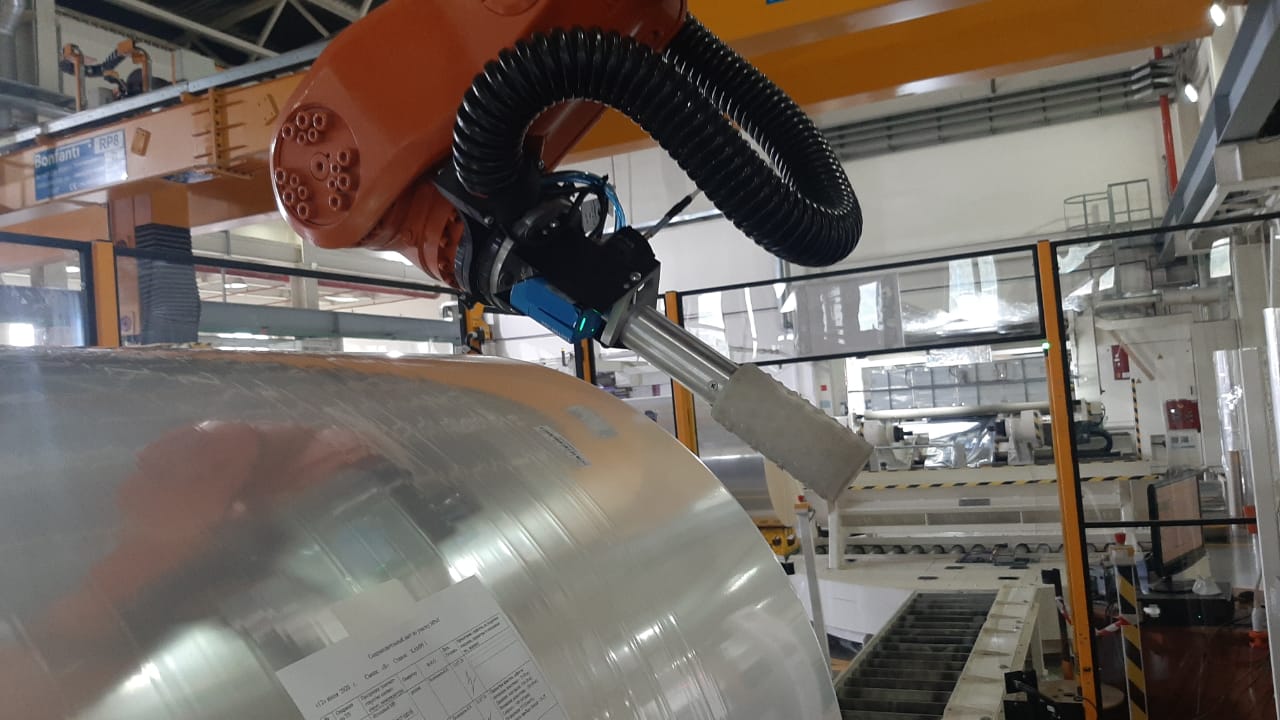
"We are implementing robotic systems for bulk raw materials unpacking, placing rubber bales in containers, attaching big bags to packaging machines, placing labels, and controlling film roll quality. Industrial robots at our facilities take on physically heavy and routine work, eliminating the need for human presence at dangerous production sites. It should be noted that special requirements for robotic system reliability and safety are characteristic of petrochemical industry. The production processes of our companies are continuous and any failure or abnormal situation can lead to line shutdowns and losses. The implemented robotic systems shall be of highest reliability and safety for employees. We work in partnership with external system integrators, and the terms of reference are developed by a corporate team of SIBUR Digital experts with extensive experience in process automation and robotics," says Alexander Semenov, Industry 4.0 Project Manager.
Robotic systems are already in operation at several SIBUR enterprises. In Voronezh, industrial manipulators put rubber pressed bales of different brands in containers after they are pre-sorted by computer vision systems. At the facility in Perm, the robot is used for stacking bags with Alphapor foaming polystyrene on pallets. In July, BIAXPLEN in Balakhna has completed commissioning of a robot that will perform polypropylene and copolymers unpacking from bags to the process line loading bins for BOPP film production. The second robotic unpacking system will be put into operation at the same facility in August 2020.
